DLP 3D Printing Technology
An advanced additive manufacturing process capable of creating highly detailed parts with exceptional precision and speed.
DLP (Digital Light Processing) 3D printing technology is an additive manufacturing process that uses a digital light projector to cure photopolymer resin. This technology is similar to SLA printing but utilizes a digital light source to project an image of the object’s cross-section onto the resin, curing an entire layer at once. DLP has gained popularity due to its speed, high resolution, and ability to produce intricate geometries with smooth finishes.
How DLP 3D Printing Technology Works
The process begins with a digital 3D model of the desired object, which is sliced into thin layers using specialized software. The sliced data is sent to the DLP printer, where a vat of liquid photopolymer resin is prepared.
The digital light projector displays the cross-sectional image of each layer, curing the resin in one go. This contrasts with SLA, which uses a laser to cure resin point by point. Once a layer is cured, the build platform moves, and the next layer is exposed until the object is fully formed.
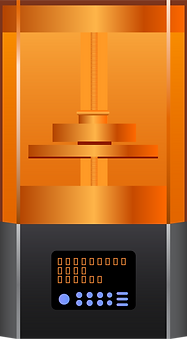
Advantages of DLP 3D Printing Technology
-
Speed: DLP cures entire layers simultaneously, making it faster than SLA for most objects.
-
High resolution: Offers excellent detail and precision, suitable for intricate parts and complex geometries.
-
Smooth surface finish: Similar to SLA, DLP produces parts with smooth, refined finishes, reducing post-processing work.
-
Material efficiency: DLP printers often use less resin compared to other methods, making them cost-effective.
Applications of DLP 3D Printing Technology
-
Dental models and prosthetics: DLP is widely used in dentistry for creating custom crowns, aligners, and prosthetics.
-
Jewelry: Perfect for creating highly detailed jewelry molds with intricate designs.
-
Medical models: Useful in creating detailed anatomical models for research and education.
-
Consumer products: Frequently used for creating high-quality prototypes and end-use components.